ERP implementations will need complex endeavors, and without careful planning and execution, they can fail to deliver the expected benefits. So what are the common reasons for ERP Failures? How to avoid this? Let’s find out with Levinci now!
Top Reasons for ERP Failures
Lack of Data cleansing
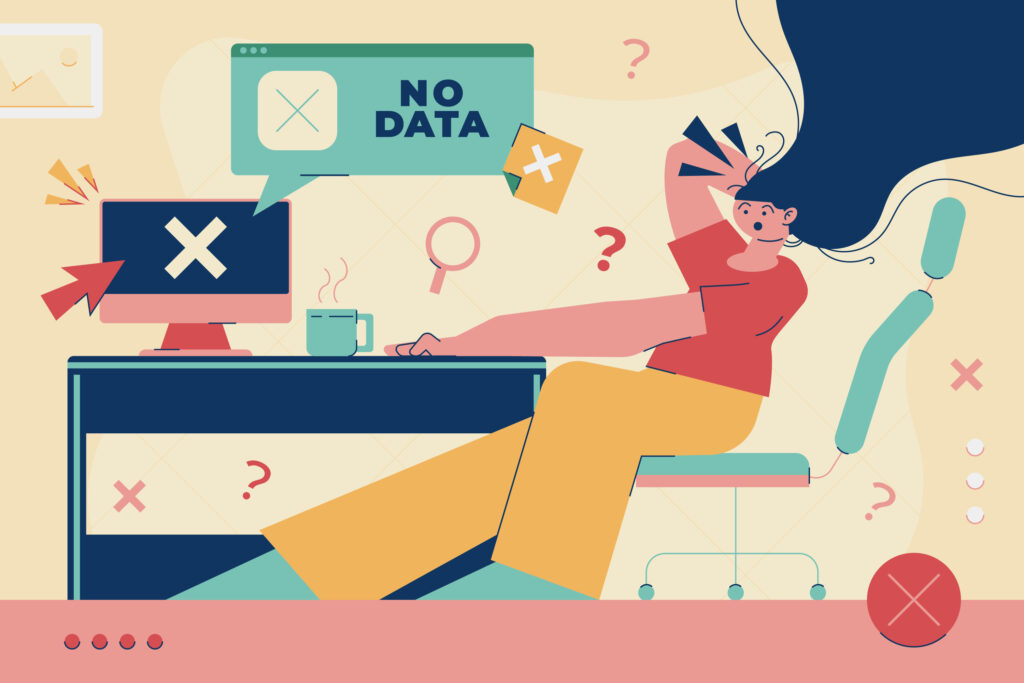
An ERP system relies on accurate data to function properly. If your legacy data is full of errors, inconsistencies, and duplicates, it will be reflected in the new system. This can lead to reporting errors, inventory problems, and difficulty in tracking orders and customers.
ERP systems need to integrate with other business systems. Dirty data can make this process difficult and time-consuming. Inaccurate data can cause errors during integration, leading to disruptions in workflows and delays, and worse will lead to ERP failures.
Fluctuating budgets
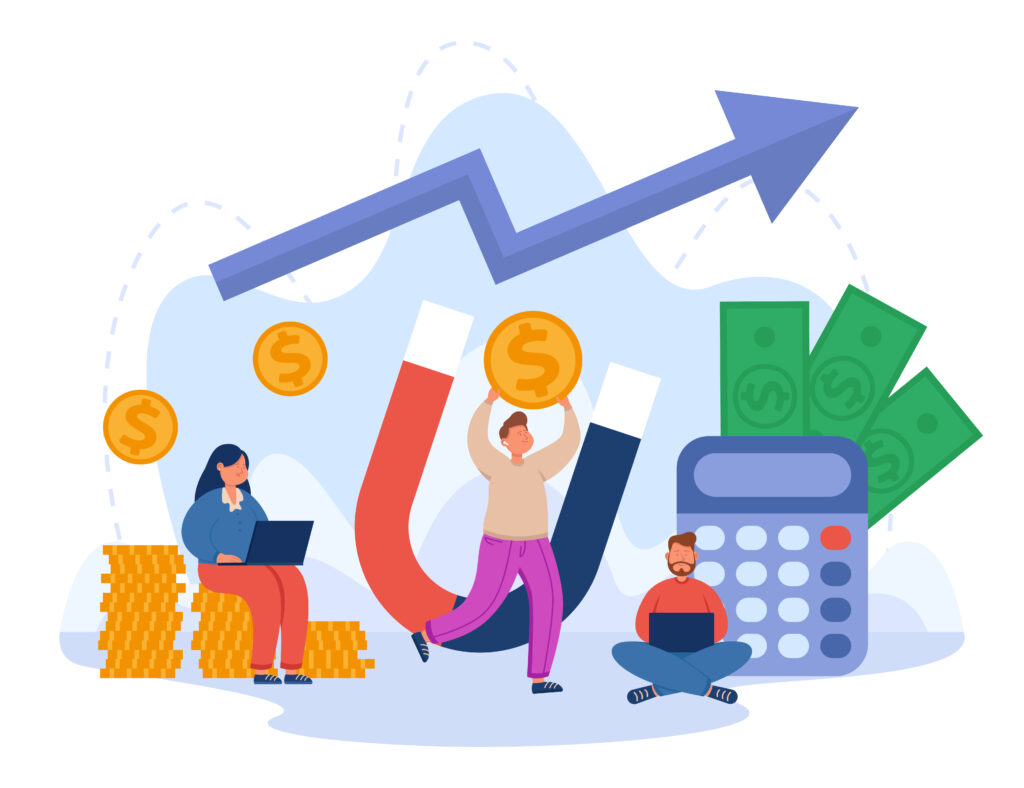
ERP implementations can be complex and require ongoing investment. If the budget fluctuates, it can be difficult to stick to the original scope of the project. This can lead to features being cut, deadlines being missed, and a system that doesn’t meet all the business needs.
In particular, fluctuating budgets can make it difficult to secure the necessary resources for the project, such as qualified consultants or additional hardware. This can slow down the implementation process and increase the overall cost.
>>> Read more: ERP Development: Stages, Benefits, and Estimated Price
Poor employee training
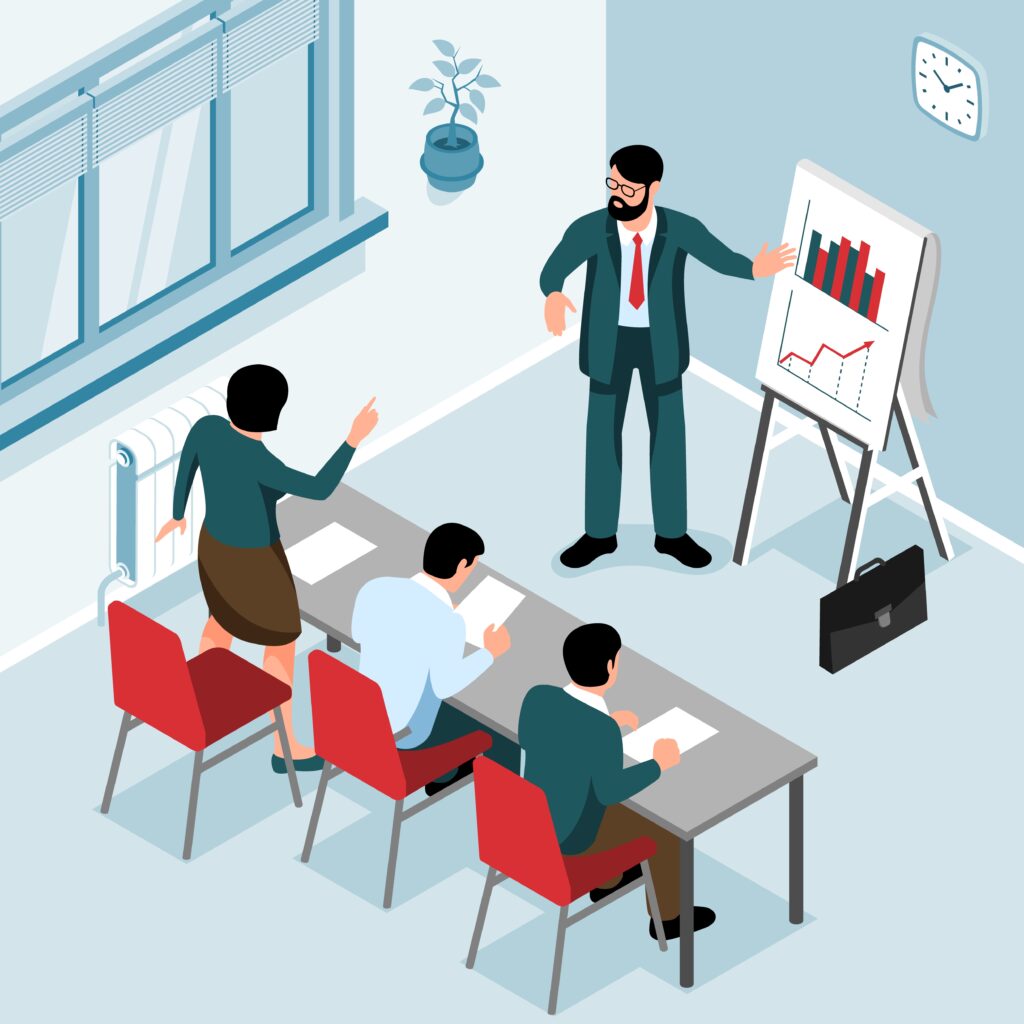
Poor employee training is a major roadblock to successful ERP implementation. If employees don’t understand how to use the new system, they’re less likely to adopt it. This can lead to continued reliance on old, inefficient processes, negating the benefits of the ERP system.
Furthermore, without proper training in data entry procedures, employees may make mistakes when entering information into the system. This can lead to inaccurate data, which can have a cascading effect on reporting, inventory management, and other critical business functions.
Poor pre-rollout testing
Poor pre-rollout testing is a significant contributor to ERP failures. Without proper testing, bugs and glitches in the system may not be identified until after the system goes live. This can lead to disruptions in operations, data corruption, and lost productivity.
In addition, ERP systems need to integrate with other business systems. Pre-rollout testing helps identify any potential integration issues that could cause errors or disruptions during the live implementation.
No change management plan
Change can be disruptive, and employees may be resistant to adopting a new system, especially if they don’t understand the benefits or feel they haven’t been properly involved in the process. Without change management procedures, communication can be haphazard and training inadequate, leaving employees confused and unprepared.
Insufficient resources
Insufficient resources can cripple an ERP implementation in several ways, hindering its success and potentially leading to outright failure. ERP systems are complex and require a team with a diverse range of skills and knowledge to implement them effectively like project management, system configuration, data migration, change management, and business process expertise.
If a company lacks the necessary resources, it can be difficult to stay on track with the project scope and meet deadlines. Important tasks may get neglected, leading to features being cut or the entire project running behind schedule. Delays can lead to frustration, decreased morale, and increased costs.
How to Avoid ERP Failures
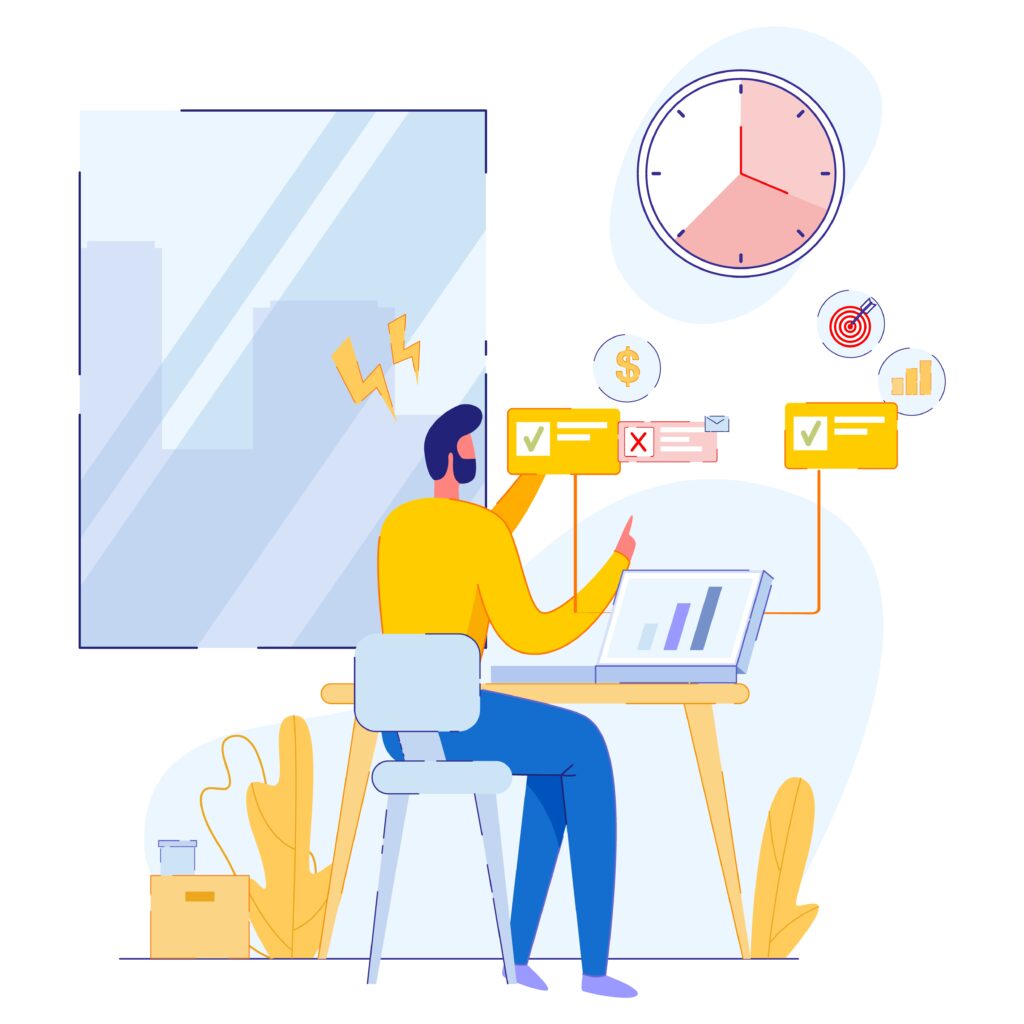
Once you have identified the causes of ERP Failures, businesses need to grasp some key strategies to avoid ERP failures and ensure a successful implementation:
Clean up data before implementing ERP
To ensure the ERP system operates smoothly, businesses need to thoroughly sanitize data. You need to make a list of all the data sources that will be migrated to the new ERP system and prioritize the data sources based on their criticality to your business operations.
You use data profiling tools to analyze your data sources and identify potential issues like missing values, inconsistencies, duplicates, and invalid characters. This will give you a clear picture of the data quality challenges you need to address.
Make specific plans and arrange enough time for the process of implementing, testing, and switching to the new ERP system
ERP Systems helps businesses simplify operating processes. However, businesses need to plan and take the time to set up and test thoroughly to be able to realize its full potential.
By creating a well-defined plan with realistic timelines and allocating sufficient resources for each stage, you can significantly increase your chances of a successful ERP implementation that meets your business goals.
For example, for the accounting department, the ERP System needs to ensure accurate reporting processes with appropriate data sources before putting it into official operation. Warehouse managers will need an ERP system to manage inventory, from the process of receiving, storing, and picking to fulfillment, all must meet the requirements.
Estimate and calculate contingency costs
ERP implementations are complex projects with inherent uncertainties. Contingency costs act as a buffer to absorb unexpected expenses and help ensure your project stays on track. In addition to the costs of implementing an ERP system, businesses need to budget for contingency costs of about 20 – 25% for any additional hardware and network infrastructure to operate the new ERP system and the costs to tailor solutions to their demands.
Train staff early
ERP systems can be complex, with new functionalities and workflows. Early training provides employees with ample time to become familiar with the system before they’re expected to use it for daily tasks. This reduces the learning curve on go-live days and minimizes disruptions to productivity. Well-trained employees can hit the ground running and start using the system effectively from the outset, maximizing its benefits for the organization.
Test everything clearly before ERP deployment
Thorough testing before cutover, also known as go-live, is crucial for a successful ERP implementation. Businesses should start testing small points of individual operational processes, followed by testing at larger workloads to pinpoint and resolve any capacity issues.
Testing ensures that all functionalities of the ERP system work as intended. This includes core functionalities, integrations with other systems, and user-specific workflows. By testing thoroughly, you can gain confidence that the system will perform its intended tasks reliably.
How much can ERP failure cost?
The cost of ERP implementation failure can be significant, ranging from hundreds of thousands to millions of dollars, depending on the size and complexity of the project. For example, a medium-sized business that implements an ERP system two weeks behind schedule due to workforce capacity issues will incur lower costs than a large corporation that discovers errors and experiences data quality problems after implementing the ERP system.
Levinci’s ERP implementation – Limit the risk of ERP failure
Levinci’s decision to implement a new ERP system is a strategic move that can streamline operations, improve data management, and boost overall efficiency. Levinci provides customized ERP system implementation solutions that fully meet the unique needs of each business. In particular, Levinci has a team of highly specialized, experienced and dedicated experts, who support you in all situations and limit the risks of ERP failures.
>>> Read more: Top ERP development companies in Vietnam 2024
Conclusion
ERP failures can happen for a variety of reasons, it is important that you know common pitfalls and take proactive steps to address them. Grow your business with the right ERP system and limit risks, contact Levinci now!
More information: